The small yet powerful plastic plug is vital in every industrial and consumer application. From safeguarding the integrity of machinery to ensuring the safety of products during transit, these components come in many shapes, sizes, and materials. Understanding their diversity is key to selecting the right plug for the job. Whether you’re a manufacturer looking to protect your products or simply curious about the ubiquity of these plastic protectors, this guide is for you. Below, you’ll find a detailed examination of plastic plugs and their relevance across different sectors.
Applications of Plastic Plugs in Various Industries
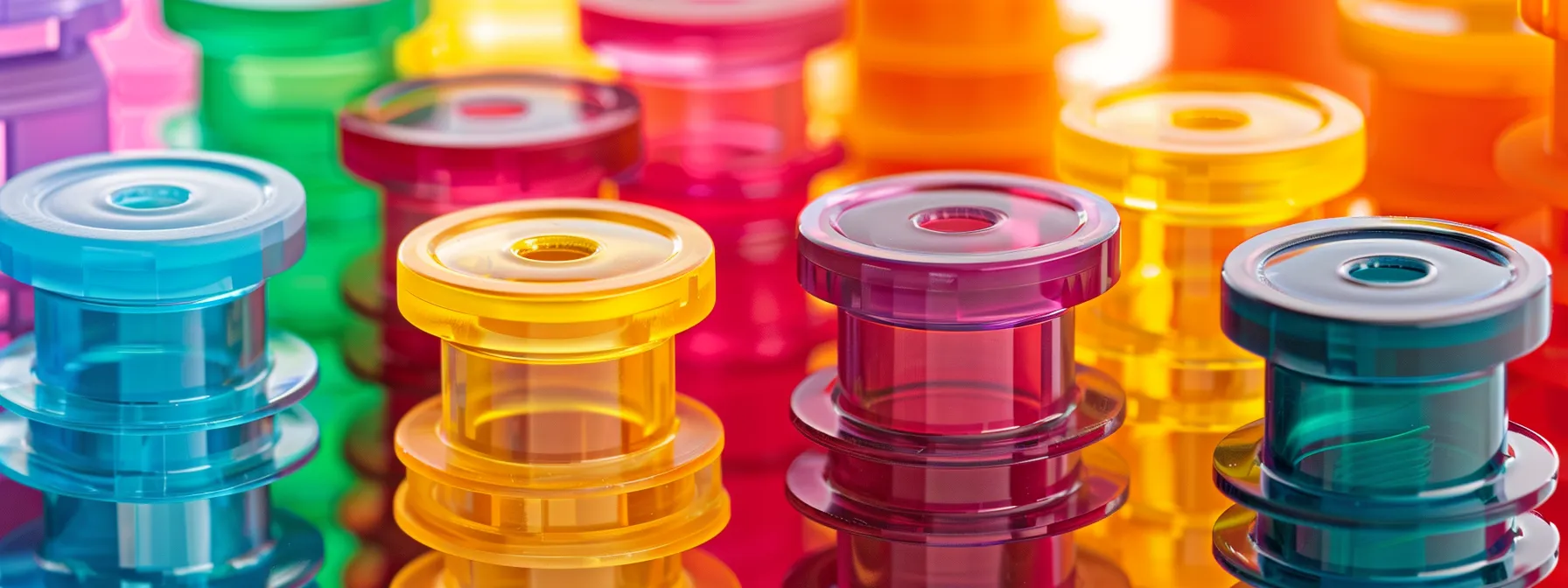
Plastic plugs are crucial components across many industries. In the automotive realm, they protect open lines and ports during manufacturing. This prevents contaminants from entering the engine block and maintains the integrity of various fluid systems.
In medicine, plastic plugs take on a more specialized role. They seal containers with life-saving drugs and shield sensitive equipment from environmental contaminants, ensuring that healthcare professionals can maintain the sterility of their instruments and the purity of medications.
Plastic plugs benefit the construction and plumbing sectors as well. They are used to cap off piping systems or temporary seals during building projects. Due to their resilience, they can withstand harsh treatment on construction sites and still provide a reliable seal for the intended applications.
Even in everyday consumer products, plastic plugs are omnipresent. They secure the ends of furniture to prevent damage during transit and act as small stoppers on household appliances. Their presence, often unnoticed, plays a significant part in the functionality and longevity of the products we use daily.
The Importance of Material Selection for Plastic Plugs
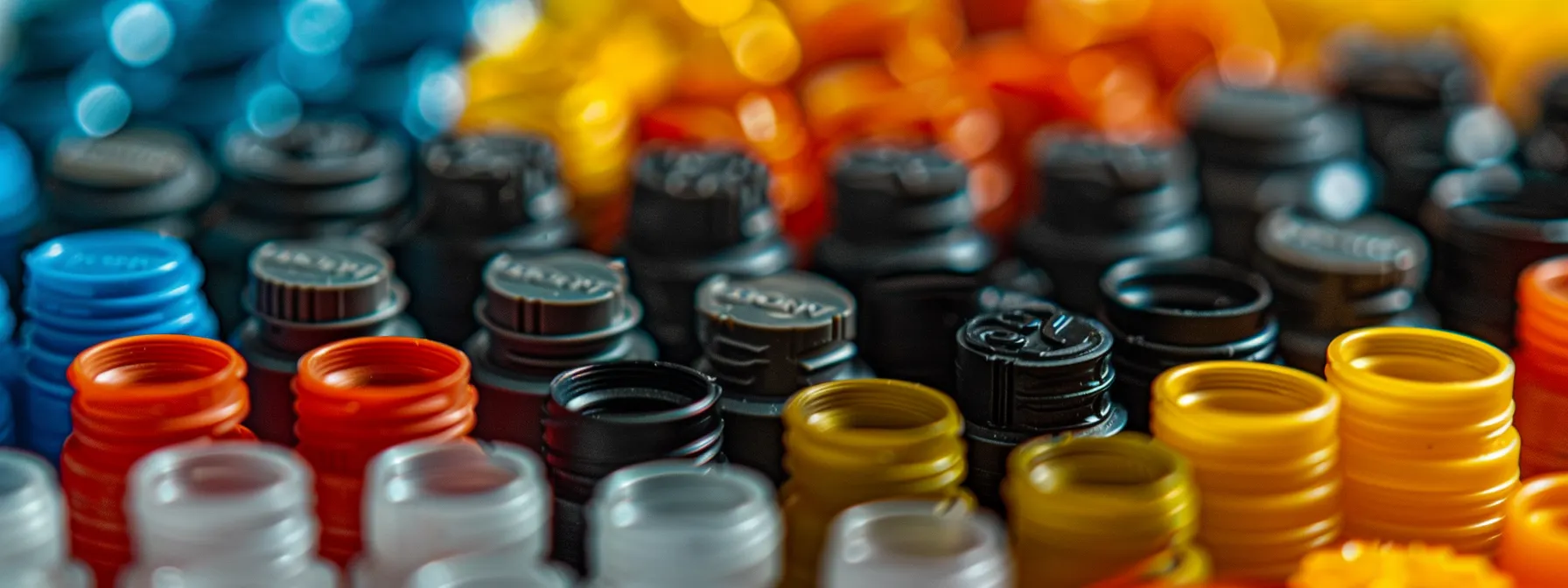
The longevity and effectiveness of a plastic plug directly correlate with the material from which it is made. Each polymer brings its own set of attributes, influencing the plug’s temperature range, chemical resistance, and structural integrity. Therefore, selecting the right material is not just a matter of preference but a critical decision in ensuring the plug’s performance.
Materials like silicone are often preferred for environments with fluctuating temperatures due to their remarkable ability to maintain their properties across a wide temperature range. Conversely, plugs made from polyvinyl chloride (PVC) or polytetrafluoroethylene (PTFE) are favored in chemically aggressive environments for their high chemical resistance.
Material innovation also contributes to plastic plugs’ environmental impact. Biodegradable materials are emerging as an alternative for those seeking to reduce their carbon footprint. This shift demonstrates an advancing consciousness in manufacturing and highlights material science’s role in evolving product design.
Manufacturers continue to experiment with material composites to enhance the features of plastic plugs. Combining different polymers or adding fillers can tailor plugs to offer heightened resistance to wear and tear, UV radiation, and other specific conditions encountered in various applications.
Innovations in Plastic Plug Designs and Functionality
Innovation within the realm of plastic plugs is driven by industries’ ever-changing demands. Modern designs reflect a trend towards multi-functionality, with plugs serving as protective barriers and integrating additional features like handles for easy removal or tabs for tampering evidence.
Smart design choices also contribute to economic and logistical efficiency. Stackable features allow for maximized storage and transportation, while color coding aids in quick identification, reducing the potential for errors in fast-paced environments like assembly lines.
A notable advancement is the incorporation of technology into plastic plugs. Some now include RFID chips or QR codes to assist with inventory management and tracking, bridging the gap between simple components and the intricate network of Industry 4.0.
The push towards designing for disassembly further demonstrates the innovation in this field. This approach ensures that the plastic plug can be easily removed and directed towards appropriate recycling streams at the end of a product’s life, encouraging circular economy principles in manufacturing.
Overall, plastic plugs are versatile and essential components across numerous industries, with innovations in material and design continually enhancing their performance and sustainability. As technology and environmental considerations evolve, these small but powerful protectors will remain critical in ensuring safety, efficiency, and longevity in various applications.